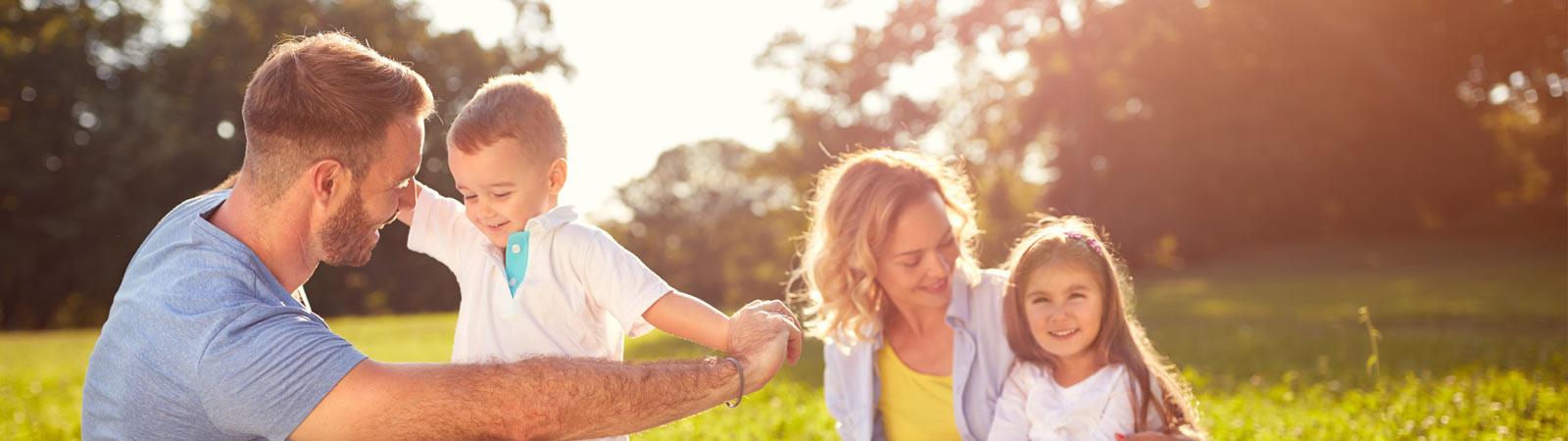
Product Safety and Quality
Ensuring the Safety and Quality of Our Products
CSL is committed to the development, manufacture and supply of high quality, safe products that save lives, improve the health and wellbeing of patients with rare and serious diseases and protect public health. Assuring the safety of our plasma donors and the quality of our starting materials, through to the manufacture, distribution, and ongoing safety surveillance of our products, is of the utmost importance to CSL.
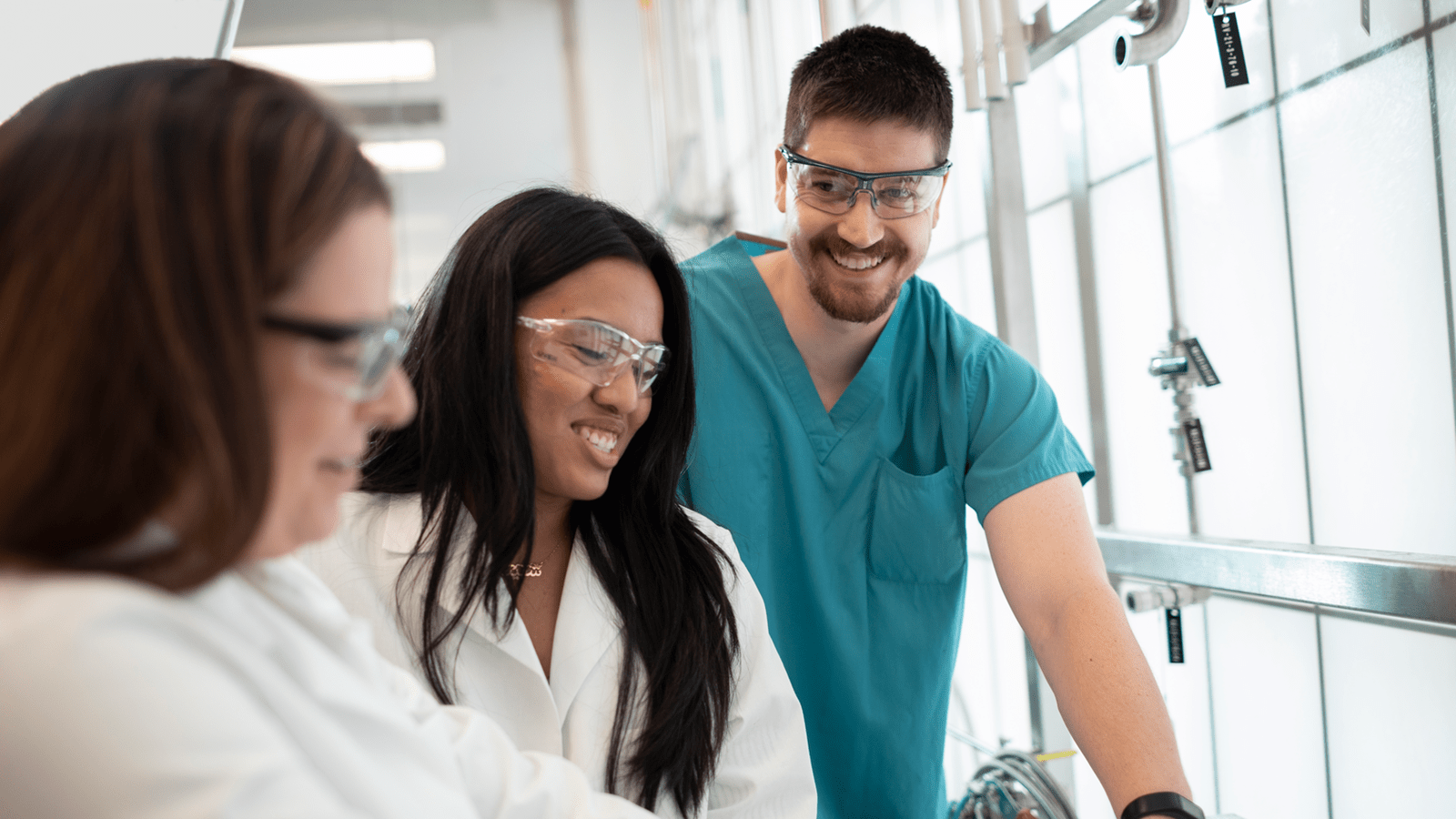
CSL’s Audit and Risk Management Committee of the Board has oversight of CSL’s systems of risk management, compliance and control, including oversight of CSL’s quality management system.
Further, CSL’s employs a dedicated quality function that strives to maintain the highest standards through the use of global quality standards, policies, procedures and electronic systems to support management of quality processes.
Our Quality Management System covers all elements of our business including:
- support of research and development (R&D) and clinical trial activities to bring new products to market;
- quality audits of, and support for, selection of suppliers;
- implementation and management of quality systems supporting each plasma centre and manufacturing site;
- oversight of third-party manufacturing partners;
- trending of quality performance via Quality Management Reviews across our businesses; and
- support for the safety and pharmacovigilance activities required to assure ongoing monitoring of product safety in the field.
Our plasma donor centres and facilities are frequently audited by regulatory agencies to ensure that our systems and products meet the requirements of applicable federal regulatory requirements. In addition, we routinely carry out internal audits together with audits of our suppliers to identify, measure and control the quality and safety of our products.
Through the entire product lifecycle – from the research and development bench through to product retirement – quality resources, processes and systems are there to support the organisation.
Safety & Manufacture Of Plasma Therapies
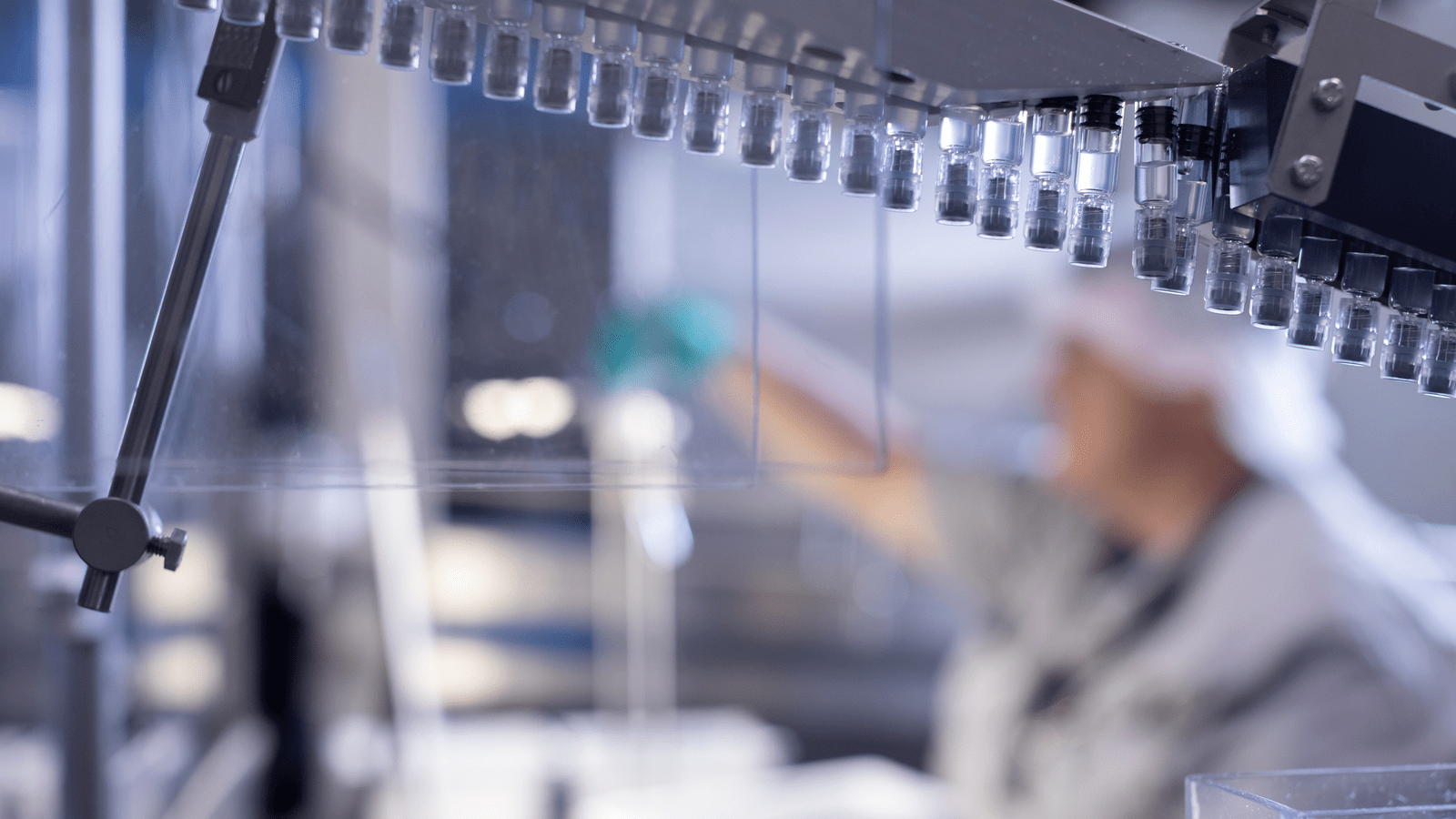
Every medicine possesses some level of safety risk. For plasma-derived therapies, the most important safety issue is the potential for contamination with pathogens originating from the plasma used to manufacture these therapies. Although the theoretical risk of pathogen transmission can never be zero, we use multiple and overlapping safety measures to reduce this risk to as low as is technically feasible. Since the introduction of dedicated virus reduction and removal steps and thorough quality assurance measures in plasma fractionation, there have been no reports of proven transmission of a pathogen via a plasma-derived therapy manufactured by CSL.
For more on safety see CSL Behring’s Commitment to Safety and Quality.
Safety & Manufacture of Vaccines
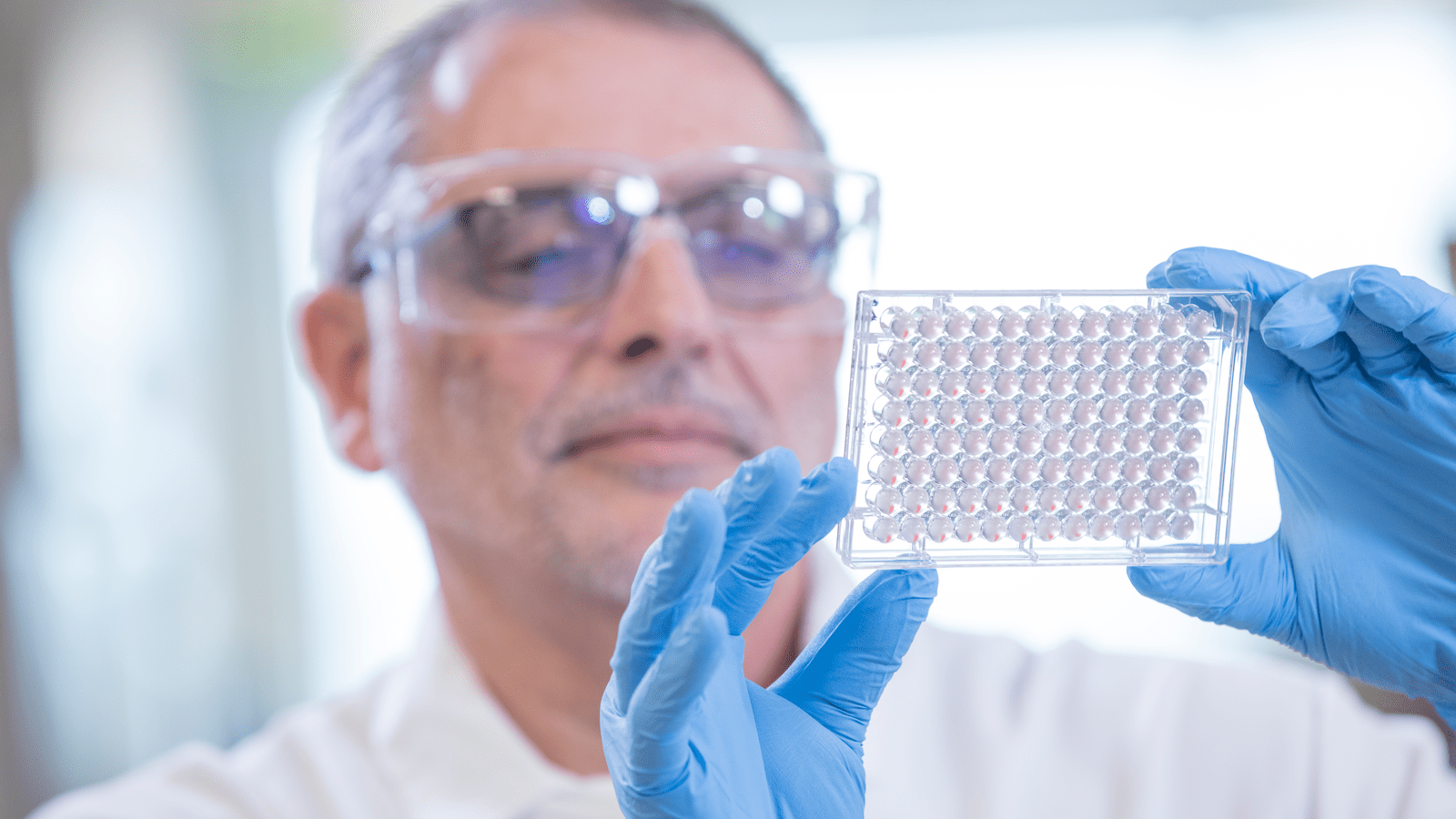
Each year, the World Health Organization (WHO) Global Influenza Network provides CSL with influenza virus samples, which represent the influenza strains predominating in the southern and northern hemispheres. The WHO and local regional authorities then make recommendations for the composition of the vaccine for the southern and northern hemispheres respectively. This ensures that the influenza strains in the vaccine match as closely as possible with the viruses that are likely to circulate in the following southern and northern hemisphere winters.
Our production plants are maintained at the highest standard and are subject to regular inspections by regulatory authorities, including the Australian Therapeutic Goods Administration (TGA), Medicines and Healthcare products Regulatory Agency (MHRA) and the US Food and Drug Administration (FDA). CSL’s Seqirus division is one of the largest influenza vaccine companies in the world and utilises both egg and cell-based production technologies, producing a broad portfolio of inactivated influenza vaccines. CSL’s egg-based influenza vaccine is an inactivated vaccine – i.e., it does not contain live influenza virus. The production process involves the use of validated procedures to chemically inactivate the virus. The safety and effectiveness of our influenza vaccine has been documented extensively in clinical studies conducted in healthy volunteers and from post-marketing surveillance in the community.
Counterfeit Medicines
The development, manufacture and controlled distribution of high-quality products is only valuable and efficacious to our patients if they actually have genuine therapies available to them via a reliable and secure supply chain.
CSL has developed and implemented a supply chain security management system that combines product and security requirements, together with loss prevention practices and anti-counterfeiting measures which establish protections throughout our supply chain. Any CSL or business partner facility engaged in the collection, manufacture, storage, handling or shipment of raw or ancillary materials, products or product data, and assets must develop and implement a risk-based, comprehensive and documented supply chain security management system.
CSL has implemented global processes to quickly respond to reports of counterfeit product and assist local law enforcement and health authorities in the investigation of counterfeit reports. These reports are managed with the highest urgency with oversight and direction provided by global policies, procedures and reporting systems that assure the right representatives from all relevant functions around the world are made aware of the situation. Resources are allocated to support confirmation of product distribution channels, batch validity and product analytical testing, as requested by authorities.
While it is virtually impossible to prevent attempts to counterfeit products, CSL has undertaken significant investment to allow for product serialisation in multiple countries. Serialisation involves the use of unique identifiers on product vials and cartons that allow for rapid verification of whether product is genuine. Where serialisation regulations and systems have been approved for implementation of serialised packaging, CSL is in full compliance with these systems.
To further protect patients, CSL has begun to package product with tamper-evident measurements, which provide visual evidence that the product has been opened, providing a high level of confidence to patients and healthcare providers that the therapies that we administer are genuine. In addition, CSL is working with health authorities to raise awareness and educate customers on how to identify, handle and report suspected counterfeit products.
To assure that products are transferred through approved, legitimate supply chain routes, CSL is prohibited from conducting business with any individual, group or organisation that has been designated on any sanction or blacklist.
Where practical, CSL participates in governmental supply chain security programs, whereby businesses are qualified by a regulatory agency, to maintain strong commitments to compliance, protecting our patients, and reducing our risk profile as CSL goods move across borders. The internal control and security infrastructure in place to support these programs reduces CSL’s risk and exposure to both internal and external supply chain interruptions, and reduces the likelihood of a loss event where CSL assets could be used in the counterfeit market.